Your critical applications
We understand that the chemical stability of your therapeutic product is vital, which is why our Type I molded glass vials are carefully designed and manufactured with the highest integrity, ideally suited to a diverse range of application needs, including:
Blood and blood components
Plasma, platelets, red blood cells, white blood cells, immunoglobulins, albumin and more are highly valuable for treating numerous diseases and protecting health.
Oncology
Drug stability and sterility are crucial for patient safety. The mechanical resistance of molded glass is particularly important to ensure the integrity of cytotoxic cancer therapies.
Antibiotics
Flexibility, integrity, and cost are essential features of glass packaging for the antibiotic supply chain – all met by our extensive Type I molded glass range of vials and infusion bottles.
Diagnostics
Diagnostic agents and contrast media are essential for diagnostic imaging. Molded glass vials are popular for parenteral contrast media due to chemical stability and inertness.
Hospital solutions
Glass packaging offers many important benefits for Standard Solutions (sterilized water, saline, and glucose) and parenteral nutrition applications in hospitals.
Animal health
Molded glass is the ideal solution for veterinary products such as injectable anti-infectives, given its practical and ergonomic design.
Respiratory
Type I glass is a popular packaging option for respiratory therapies, notably for nasal drug products and parenteral vials, owing to its superior mechanical resistance.
Quality Policy
Commitment & Accountabilities
SGD Pharma is committed to protecting and improving patient health by providing high quality, reliable and innovative products to our customers in the pharmaceutical industry.
Part of our mission is putting patient health as the top priority when we are making decisions.
All employees and external contributors work to meet SGD Pharma quality objectives. Each participant involved in the production of our glass vials, bottles and ampoules is held directly responsible for the quality of the product that is being made.
Put our customers at the heart of our priorities
Put our customers at the heart of our priorities
- Ensure that each employee understands the needs of our customers and the pharmaceutical industry.
- Be recognized by our customers for reliability in the quality of our products and service.
- Provide fast and efficient technical support.
Incorporate the requirements of the pharmaceutical industry
Incorporate the requirements of the pharmaceutical industry
- Maintain ISO 15378 certification at all our sites, according to the rules of Good Manufacturing Practices applicable to primary packaging in the pharmaceutical industry.
- Verify the proper application of relevant regulations and standards at appropriate intervals.
- Be vigilant with regard to regulatory changes related to bottles in the pharmaceutical industry through proactive monitoring.
Develop our skills
Develop our skills
- Ensure that each employee is fully aware of SGD Pharma’s quality objectives and takes an active part in achieving the targets set.
- Regularly evaluate employee skills and qualifications and plan the actions necessary to ensure that an adequate level is maintained.
- Train each employee to build on their skills to achieve our required quality objectives.
Move towards zero defects
Move towards zero defects
- Complete quality performance reviews at Group level and at each site to define an action plan, taking into account data analysis and the results of quality and customer service indicators.
- Evaluate the risks of non-conformity by using adapted tools (change control, FMEA study), allowing the implementation of preventive actions.
- Improve the robustness of our processes by systematically using problem-solving methods.
Regulatory Affairs
International standards
- ISO 15378 Standard
- International Standard for Phytosanitary Measures 15 (ISPM 15) on wood materials
Pharmacopoeial guidance
- European Pharmacopeia: Chapter 3.2.1
- United States Pharmacopeia: USP <660>
- Japanese Pharmacopeia: Chapter 7.01 method 1
- Chinese Pharmacopeia: YBB
EU Regulations and Directive
- EU Directive 94/62/EC on “Packaging and packaging waste”
- EU Regulation 1907/2006/EC (REACH Regulation) on “Registration, Evaluation, Authorisation and Restriction of Chemicals”
- EU Regulation 1935/2004/EC on “materials and articles intended to come into contact with food”
- EU Directive 84/500/EC and its amendments on “ceramic articles intended to come into contact with foodstuffs”
- EU Note for guidance EMA/410/01 on “minimising the risk of transmitting animal spongiform encephalopathy agents via human and veterinary medicinal products”
About us
Key facts
Business data
Turnover: 450 M€ (2024)
Global production capacity:
+ 8 Million vials per day
5 plants
7 furnaces
1 sorting facility
1 decoration workshop
Geographical areas: worldwide scope
90 agents & distributors
10 sales offices
Products’ categories & market applications:
Parenteral: molded injectable vials, tubular injectable vials, infusion bottles, ampoules
Oral: syrup bottles, tablet bottles, aerosol bottles, single dose bottle, droppers, bottles for antibiotics with filling mark
Baby bottles
Nasal bottles
Diagnostic bottles
Special needs: New designs & Innovation, plastic coating & printing, internal siliconization, ready-to-use, complete packs
Vials are carefully designed and manufactured with the highest integrity, ideally suited to a diverse range of application needs.
Social data
3063 employees
30% of women in top
management positions
245 person recruited in 2023
25,5 hours of training per employee per year
Environmental data
-18%
water consumption
-1,5%
GHG emissions on our European perimeter
+ 41%
of recycled waste
Milestones
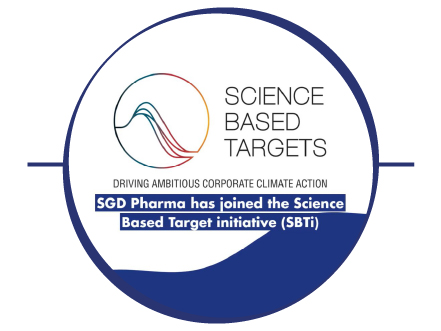
Our CSR strategy
To minimize the impact of our business on the environment, we are prioritizing decarbonization. Our goal is to lead the pharmaceutical glass manufacturing industry with our decarbonization efforts, with the intention of reducing CO2 emissions by 35% by 2030 and by 65% by 2040. SGD Pharma is SBTI committed and currently working on the 1.5°C scenario decarbonation pathway validation including our scope 3 emissions.
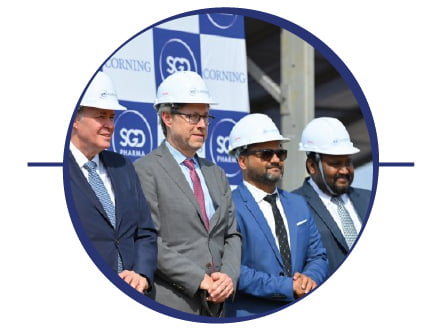
Tubular and Corning partnership
SGD Pharma announced a joint venture with Corning to adopt the company’s Velocity® Vial coating technology and manufacture high-quality tubular vials at a new tube manufacturing facility in construction at SGD Pharma’s Vemula India production site.
This collaboration will help pharma companies respond to increasingly complex capacity and quality issues while meeting global demand for critical medicines. We broke ground on the $60M site in June 2023.
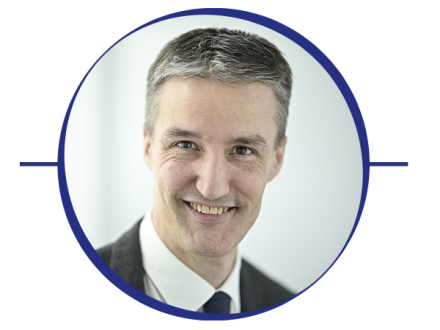
Olivier Rousseau appointed as new Chief Executive Officer
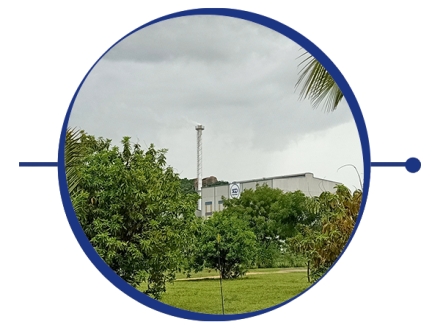
Inauguration of SGD Pharma India plant’s Unit V, fully dedicated to tubular glass packaging (capacity of 1 billion pieces by 2024).
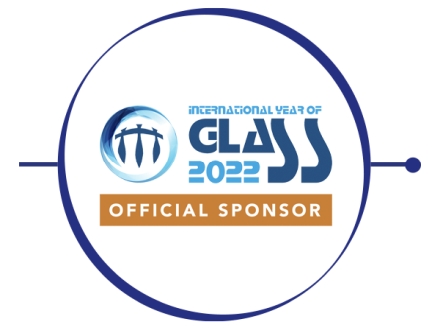
The United Nations (UN) recognizes glass as an essential material and that this year, its contribution to society will be honored through the International Year of Glass 2022. SGD Pharma, as an official sponsor of the UN International Year of the Glass, will be spotlighting glass and its role in health and wellbeing.
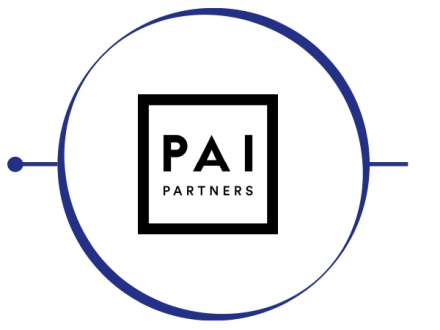
PAI Partners (PAI), a leading European private equity firm, becomes SGD Pharma new shareholder.

Ecovadis Platinum medal - The group was awarded the Ecovadis Platinum medal, its Chinese plant and its subsidiary Embelia were both awarded the Silver medal.
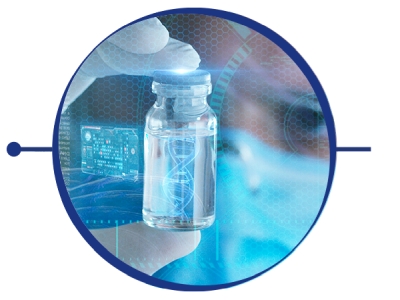
Introduction of Type I molded glass enhanced offer: three distinct solutions - AXess, AXecure and AXpert - to help customers make an optimized choice, well-matched for specific requirements.
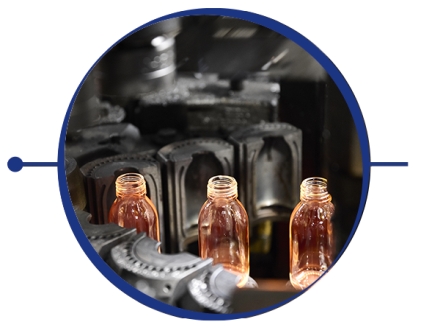
SGD Pharma starts a major Sucy-en-Brie plant development project, investing over 31M€ to rebuild one of the furnaces and modernize the site.
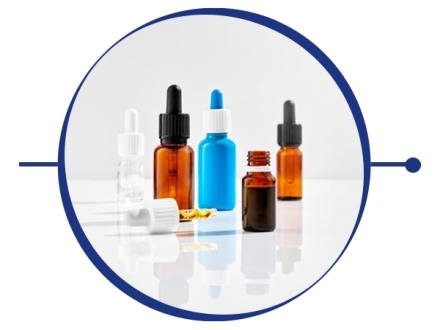
Introduction of Ensiemo, the new complete child-resistant packaging solution for CBD oils. Combining the company’s extensive pharmaceutical packaging expertise with the need for compliant, safe packaging for CBD oils, SGD Pharma has developed its first complete packaging solution & services, Ensiemo: a wide range of dropper bottles and dropper, in clear or amber glass.
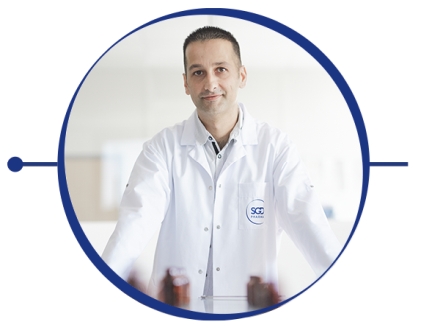
As part of its continuous improvement program, SGD Pharma optimized in 2020 the clear Type I glass composition of its best-in-class manufacturing plant at Saint-Quentin-Lamotte. This implementation provides a more robust process to improve the stability of the glass quality, improves the chemical resistance to reduce interaction with sensitive drug formulation and answers to stricter regulatory requirements.
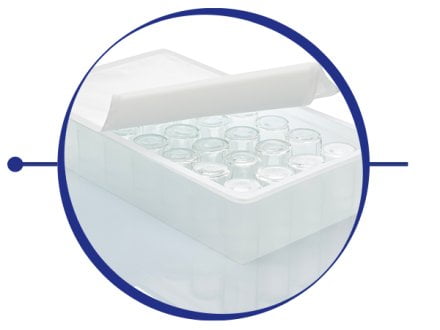
Introduction of Sterinity. The Sterinity platform in partnership with Stevanato Group – a recognized RTU platform for injectable vials by the pharmaceutical industry - offers high quality pre-sterilized Type I molded glass to speed up aseptic filling processes and reduces time-to-market for high value parenteral drugs.
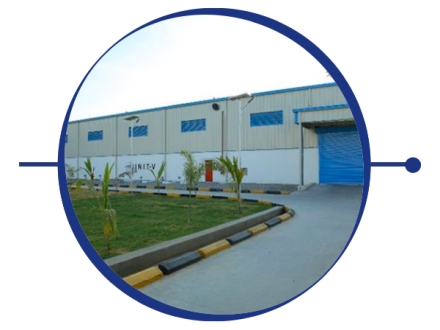
India plant's new Unit V is fully operational and 100% dedicated to our tubular product range.
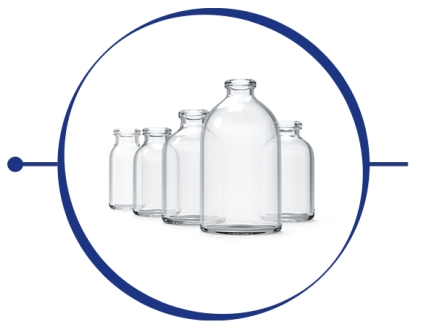
Launch of Clareo. This new innovative range of vials offers a combination of homogeneous wall thickness and superior cosmetic quality, which is unique for the molded glass Type II market. Improved mechanical resistance, significant reduction in the breakage rate and improved inspectability are the main characteristics of Clareo.
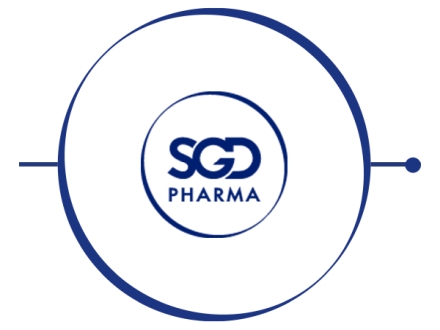
SGD Pharma unveils its new identity. The new mission, vision and guiding principles support an ambitious growth strategy and a long-term vision for SGD Pharma.
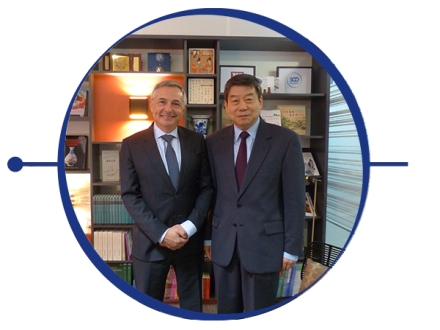
JIC (China Jianyin Investment Ltd) becomes SGD Group new shareholder.
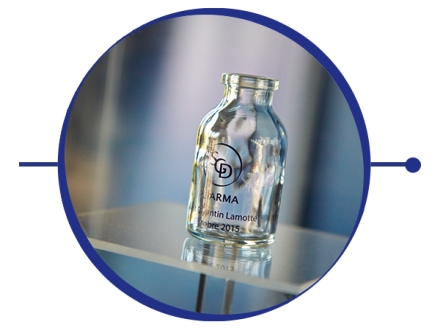
The new plant at Saint-Quentin-Lamotte produces its first glass vial on September 11th. December 21st marks the end of the pharmaceutical glass production at Mers-les-Bains after 57 years dedicated to this activity.
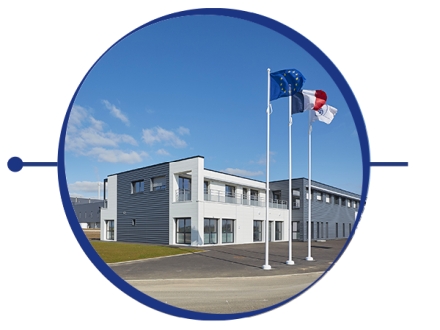
New manufacturing factory in Picardie at Saint-Quentin-Lamotte. SGD launched the newest, most modern plant in the world to manufacture molded glass pharmaceutical packaging. The construction lasted 13 months. The 13-hectare site benefits from a state-of-the art equipment (electrical and oxy-gaz furnaces) enabling an outage daily capacity of 1 million bottles and 20.000 tons per year.
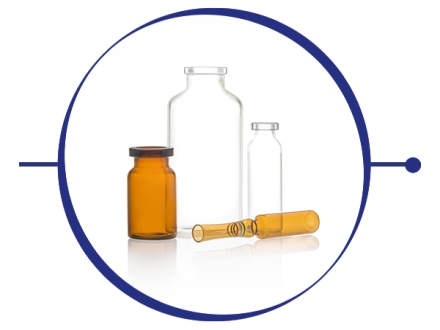
The acquisition of an India-based manufacturer of Type I allows SGD Pharma to enter the tubular conversion market and to serve the fast-growing Indian pharmaceutical market.
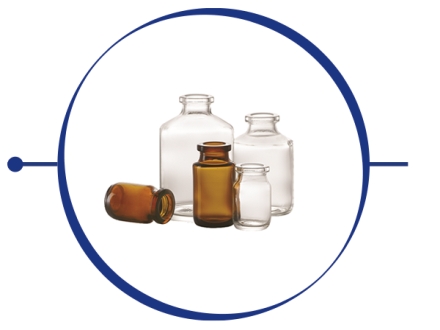
Introduction of EasyLyo. EasyLyo provides a stronger packaging that is more resistant and suitable to extreme conditions encountered during the lyophilization process. EasyLyo is a range of Type I glass vials combining the strength of molded glass with superior cosmetic quality and weight reduction.
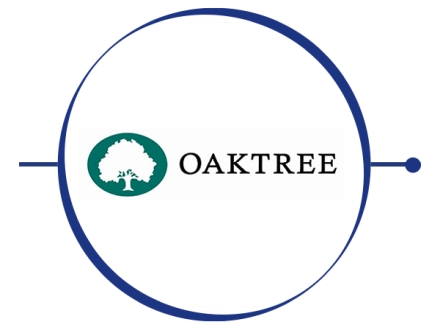
Oaktree Capital Management Ltd, an American investment firm, enters the Group’s capital on February 4th.
---Sorting-of-pharmaceutical-glass-packaging.jpg)
Acquisition of the Société de Services Verriers (SSV) company in France, dedicated to the sorting of pharmaceutical containers, which is a new activity for SGD Pharma.
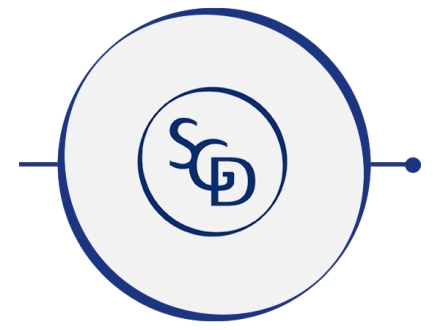
Saint-Gobain Desjonquères becomes SGD Group. SGD Pharma is the first molded glass manufacturer to obtain the ISO 15378 certifications for all its pharmacy sites.
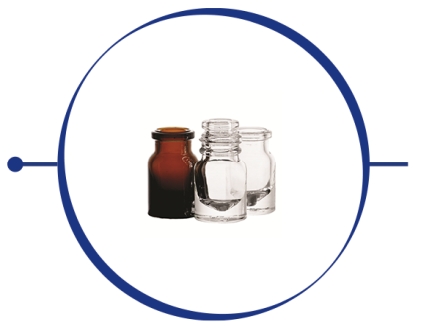
U-Save launch. The U-Save range is dedicated to nasal applications. The specific design of the U-Save molded vials provides 100% of product recovery for high value nasal spray drugs. Can be customised with plastic coating and/or decoration.
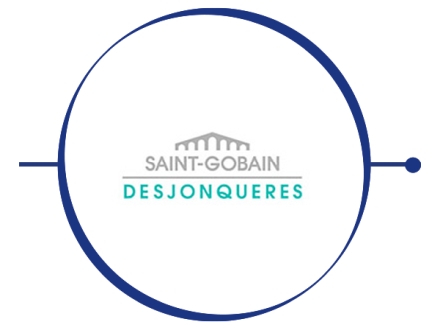
The acquisition of the Henri Desjonquères company by Saint-Gobain gives birth to Saint-Gobain Desjonquères, increasing its number of manufacturing sites worldwide: Kipfenberg (Germany), Santa Marina (Brazil), La Granja (Spain).
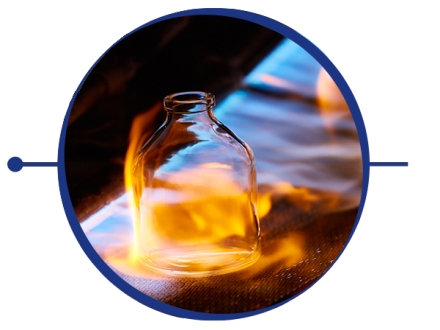
The furnace 4 at the Mers-les-Bains (France) factory is dedicated to the production of Type I molded glass.
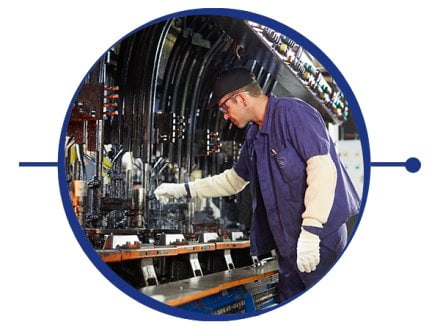
Automation of the Mers-les-Bains (France) factory with IS machines.

Specialization of the factory in Sucy-en-Brie (France) in the production of pharmaceutical bottles in molded glass.
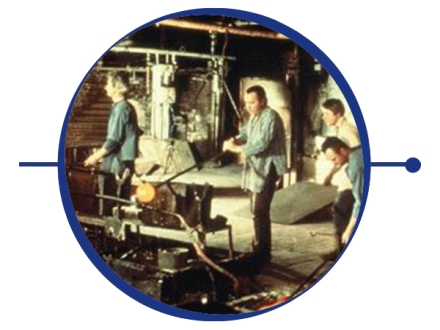
Henri Desjonquères founds Verrerie du Tréport, a glass manufacture factory in Mers-les-Bains (France), primarily aimed at the luxury perfumery market. The molded glass bottles are hand-blown.
Corporate strategy
OUR MISSION
Improve and protect patient’s health by providing high quality, reliable, and innovative primary glass packaging to our pharmaceutical customers
OUR VALUES
DEVELOP PEOPLE & TALENTS
We train, develop and invest in our people
We strive to create a positive work atmosphere
We recognize both leadership and expertise as career paths to grow in the company
OUR VALUES
PARTNER WITH THE CUSTOMER
We build long-term relationships with our customers
We are agile and responsive to customer’s needs
We optimize customer experience by being reliable and transparent
We innovate in collaboration with our customers to improve our offering
OUR VALUES
COMMIT TO PATIENT SAFETY
We understand our critical role in delivering drugs to patients safely
We put the highest focus on the quality provided to our customers
We consistently apply GMP standards
Protecting children with lifesaving packaging
An evaluation of current and future child-resistant packaging trends in the pharmaceutical industry
Understand the evolving child-resistant packaging market and current regulations
Despite a reduction in cases in recent years, unintentional child poisoning remains a considerable risk in the home, with over-the-counter and prescription medicines presenting the greatest risk. Patients and stakeholders are calling upon the pharmaceutical industry to recognize the importance of child-resistant closures (CRCs) in medical packaging that is effective at preventing young children opening medication, while remaining accessible to senior patients.